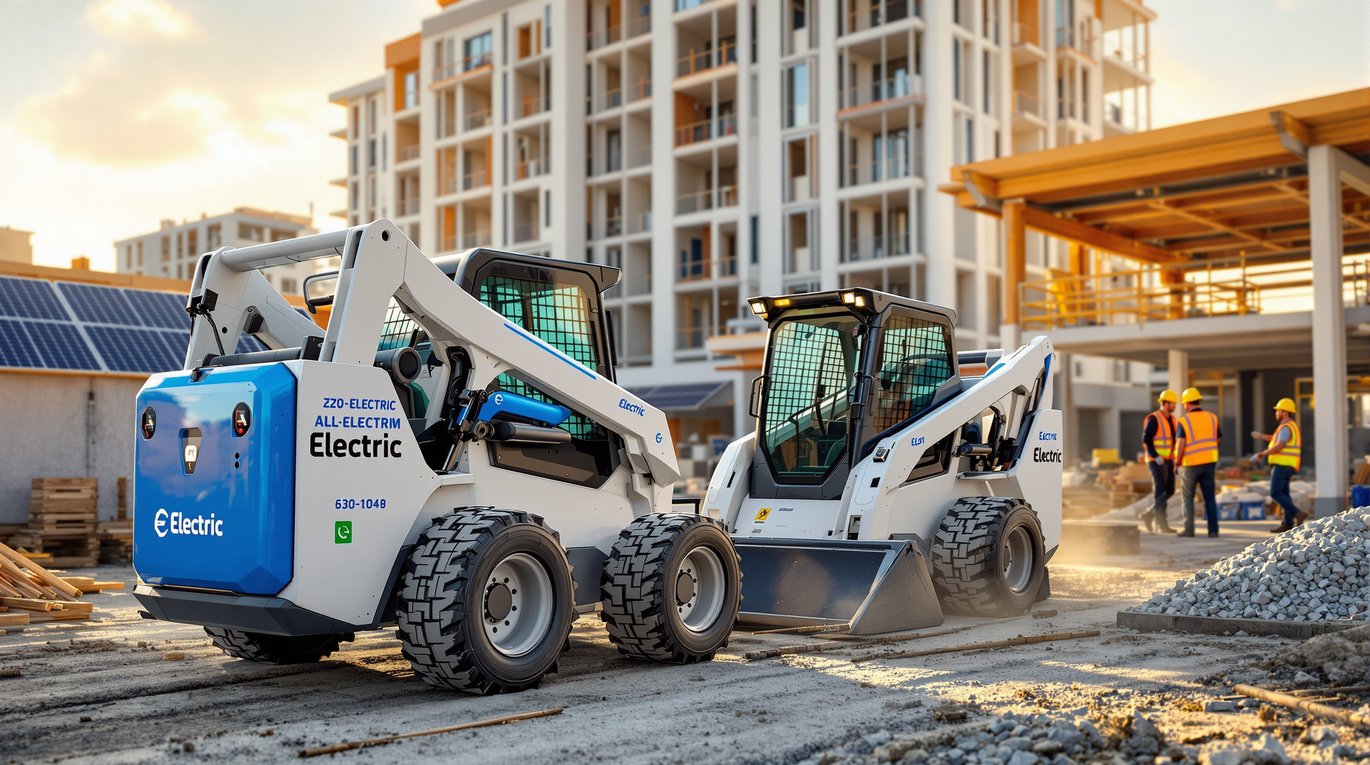
Construction site productivity depends heavily on equipment selection. Traditional diesel-powered machines have served the industry well, but electric skid loaders are now reshaping job site operations.
The skid steer loader industry has made remarkable strides, especially when you have lower operating costs and better efficiency. Electric skid steer prices now compete effectively with traditional options and construction companies can upgrade their fleets affordably. These innovative machines streamline construction sites through better performance, lower costs, and environmental advantages.
Let's get into the technology behind electric skid loaders, understand their operational benefits, and break down the costs versus benefits to help you make smart decisions for your construction projects.
Understanding Electric Skid Loader Technology
Electric skid technology shows remarkable progress as manufacturers develop two distinct approaches: battery-electric and all-electric systems. Let's look at the core technologies behind these state-of-the-art developments.
Key Components of Electric Systems
Modern electric skid loaders feature a sophisticated powertrain system at their core. The Bobcat T7X showcases a powerful 72.6-kilowatt-hour lithium-ion battery system with impressive performance metrics. These machines operate with all but one of these components compared to traditional diesel counterparts.
All-electric models showcase a groundbreaking advancement by eliminating hydraulic systems. Electric actuators replace traditional hydraulic components for lift and tilt functions. This results in precise control and less maintenance.
Battery Technology and Power Management
Electric skid loaders' battery technology has advanced remarkably. Smart power management systems detect workload requirements and deliver electrical power as needed. Battery life remains preserved while performance stays optimal, and some models run up to eight hours continuously.
Modern electric skid loader batteries feature these specs:
- Lithium-ion chemistry for consistent power delivery
- Operating voltages up to 465V
- Intelligent power management for extended runtime
- Instant torque delivery up to three times greater than traditional loaders
Charging Infrastructure Requirements
Electric skid loaders offer three main charging levels:
Charging Level | Voltage | Charging Time |
Level 1 | 120V AC | Up to 24 hours |
Level 2 | 240V AC | 8-12 hours |
Level 3 | 480V DC | 2-3 hours |
Charging infrastructure needs careful planning. Operators need a dedicated Level 2 charging setup with a 240V, 40-amp circuit installation. Commercial operations now benefit from mobile charging solutions and solar-powered options that work well on remote job sites.
These machines' power management systems preserve energy by delivering power only when tasks demand it. This smart approach extends runtime while maintaining peak performance levels.
Maximizing Operational Efficiency
Proper operational practices determine the efficiency and longevity of electrical skid equipment. Let's examine ways to get peak performance from these powerful machines.
Optimal Work Patterns for Battery Life
Smart charging practices substantially affect battery longevity. Battery life extends while performance remains consistent when charge levels stay between 20% and 90%. Equipment operators should charge during natural breaks like lunch hours instead of waiting until batteries are empty.
Latest electric skid loaders work for up to four hours continuously or throughout intermittent daily use. Runtime optimization requires:
- Power modes that match task requirements
- Regular charging schedules during breaks
- Battery temperature monitoring during operation
- Prevention of complete battery depletion
Smart Power Management Techniques
Power management capabilities come standard with modern electrical skid systems. The T7X model offers three distinct power modes:
Mode | Application | Power Output |
Eco | Light tasks | Minimal power usage |
Normal | Standard operations | Balanced output |
Peak | Heavy-duty work | Maximum performance |
These smart systems deliver up to three times greater torque than traditional loaders while maintaining optimal efficiency. Task-specific power mode selection reduces energy consumption without compromising performance.
Performance Monitoring Systems
Systems like Machine IQ show immediate equipment performance data. These systems monitor essential metrics including:
- Operating hours and fuel efficiency
- Battery health and charging cycles
- Location tracking and utilization rates
- Maintenance schedules and alerts
Compared to diesel counterparts, monitoring systems can reduce maintenance costs by up to 70%. Evidence-based data helps predict maintenance needs and optimize charging schedules. This ensures maximum uptime for electrical skid equipment.
These advanced monitoring capabilities enable better decisions about equipment deployment and maintenance scheduling. The result is improved operational efficiency across the board.
Cost-Benefit Analysis
The financial aspects of electrical skid equipment reveal a complete cost picture that helps make informed decisions. Our analysis shows surprising facts about these innovative machines' long-term economics.
Original Investment vs Long-term Savings
The electric skid steer price runs 20-35% higher than traditional diesel models. This upfront premium gets offset by operational savings quickly. A smart investment decision looks beyond the purchase price to factor the equipment's total lifecycle costs and potential returns.
Electric skid loaders achieve payback within approximately 18 months through reduced operating expenses. These machines deliver exceptional returns while maintaining their durability and longevity.
Maintenance Cost Reduction
Electric skid equipment needs much less maintenance. Here are the advantages:
- 50% fewer components compared to diesel models
- 96% reduction in fluid requirements
- No engine oil changes or filter replacements needed
- Simplified troubleshooting due to fewer mechanical parts
Energy Cost Comparison
The documented energy cost savings stand out clearly. Annual operating costs based on 750 hours of operation show:
Cost Category | Electric Skid | Diesel Skid |
Annual Energy/Fuel | [USD 810 | USD 12,960](https://attachmentsking.com/blogs/guides/should-i-buy-an-electric-skid-steer?srsltid=AfmBOoriqzq215m0GroW2MiKkNFtfQomDeS0PXgfAXWWi3Z8iFC_dnAV) |
Hourly Operation | USD 0.33 | USD 3.04 |
These numbers explain why construction companies of all sizes adopt electrical equipment skid systems rapidly. Electric models use approximately 2kW per hour, which results in an operational cost of USD 0.33 per hour.
Electric skid steers eliminate idle-time fuel consumption, a major cost factor in traditional diesel equipment. The machine uses no energy when inactive, unlike diesel models that burn fuel even at idle.
The skid steer loader industry experiences a fundamental change as these benefits become widely known. Contractors achieve up to 70% reduction in operating costs compared to diesel alternatives. This makes electric equipment an attractive choice for construction operations of all sizes.
Productivity Enhancements
Our extensive testing of electrical skid systems shows productivity gains that go way beyond simple operational improvements. Recent breakthroughs have revolutionized our approach to construction tasks. These systems now provide unprecedented control and efficiency.
Faster Response Times and Controls
Modern electric skid loaders deliver instantaneous torque that's up to three times greater than traditional machines. This remarkable responsiveness results in more precise operations and faster cycle times. The control system provides three distinct modes:
Control Mode | Application | Response Time |
Eco Mode | Precise Operations | Gradual Response |
Normal Mode | Standard Tasks | Balanced Control |
Peak Mode | Heavy-Duty Work | Instant Feedback |
Reduced Downtime Benefits
Electric equipment skid systems have shown remarkable improvements in operational efficiency. These machines use about 50% fewer components than their diesel counterparts. This reduction directly leads to less maintenance-related downtime. The benefits we see are impressive:
- Elimination of traditional hydraulic system maintenance
- No engine warm-up period required for cold weather operations
- Instant climate control activation for operator comfort
Multi-tasking Capabilities
The most important advancement we see is knowing how to perform multiple functions simultaneously. Latest electric skid steer models can drive, lift, and tilt simultaneously without any noticeable power lag. This capability marks a major step forward in operational efficiency.
These machines maintain full power output even during multiple simultaneous tasks - something traditional hydraulic systems couldn't achieve. The intelligent power management system distributes energy optimally. Operators can stay productive even during complex operations.
Electric skid steer loader technology has made remarkable progress in control precision. Electric actuation now replaces hydraulic systems, which results in more accurate cylinder positioning and better overall machine control. This improved precision helps complete delicate tasks efficiently and reduces operator fatigue.
The impact on electric skid steer operating cost per hour is remarkable. Operators can complete jobs faster and more efficiently than ever before because they can perform multiple tasks simultaneously with instant electric system response. They maintain peak productivity throughout their shifts, thanks to reduced vibration and noise levels.
Environmental Impact and Compliance
Electric skid systems have revolutionized eco-friendly construction methods. These machines do more than reduce our carbon footprint—they have changed how we work in environmentally sensitive areas.
Zero Emission Benefits
Our work with electric skid loaders shows remarkable environmental improvements. These machines create zero emissions while operating, which makes them perfect for indoor and outdoor use. This becomes especially valuable when we work in enclosed spaces or environmentally sensitive areas where diesel equipment isn't allowed.
The effects go beyond emissions. We see a big deal as it means that 96% reduction in fluid usage compared to diesel machines. This brings:
- Minimal risk of ground contamination
- Reduced environmental cleanup costs
- Lower environmental compliance overhead
- Improved safety in sensitive ecosystems
Noise Reduction Advantages
The sort of thing i love about these systems is their quiet operation. Modern electrical equipment skid systems run at noise levels up to six times lower than regular diesel equipment. Here's a comparison of noise levels in different conditions:
Operation Type | Electric Skid | Diesel Skid |
Idle | Near Silent | 85+ dB |
Standard Operation | Minimal Noise | 95+ dB |
Heavy Usage | Reduced Vibration | 105+ dB |
This quieter operation lets us:
- Work in noise-sensitive areas
- Extend operating hours in urban environments
- Improve operator comfort and reduce fatigue
- Maintain better communication on job sites
Meeting Environmental Regulations
Electric skid steer technology fits perfectly with stricter environmental regulations. The skid steer loader industry faces tighter emissions controls, and our electric models already exceed these requirements.
Zero-emission operation helps us follow strict urban construction rules, especially in areas with noise limits near schools, hospitals, and residential zones. Many cities now have noise rules that restrict construction equipment use, but our electric skid steers let us work within these limits while staying productive.
These machines excel at meeting indoor air quality standards. Their zero emissions and minimal noise mean we can work in enclosed spaces without extra ventilation. This opens new opportunities for interior demolition and renovation projects where diesel equipment wouldn't work.
Environmental benefits improve our bottom line through lower compliance costs and expanded operating options. The electric skid steer's higher price often pays off because we can bid on environmentally sensitive projects that wouldn't be possible with standard equipment.
Conclusion
Electric skid loaders are revolutionizing modern construction sites. These machines help companies save money through reduced maintenance, lower energy costs, and minimal downtime. Their sophisticated power management systems and advanced controls respond three times faster than traditional equipment.
The numbers tell an interesting story. The higher upfront cost becomes a smart investment as operators see positive returns within 18 months through lower operating costs and increased efficiency. These machines are a great way to get value, especially when you have projects with strict emissions and noise requirements.
The construction equipment market keeps changing. Electric skid loaders are pioneering this shift by combining power, precision, and sustainability that today's construction needs. The technology might look complex, but the real-world benefits of lower costs, better efficiency, and environmental compliance make electric skid loaders worth thinking over for any construction fleet upgrade.