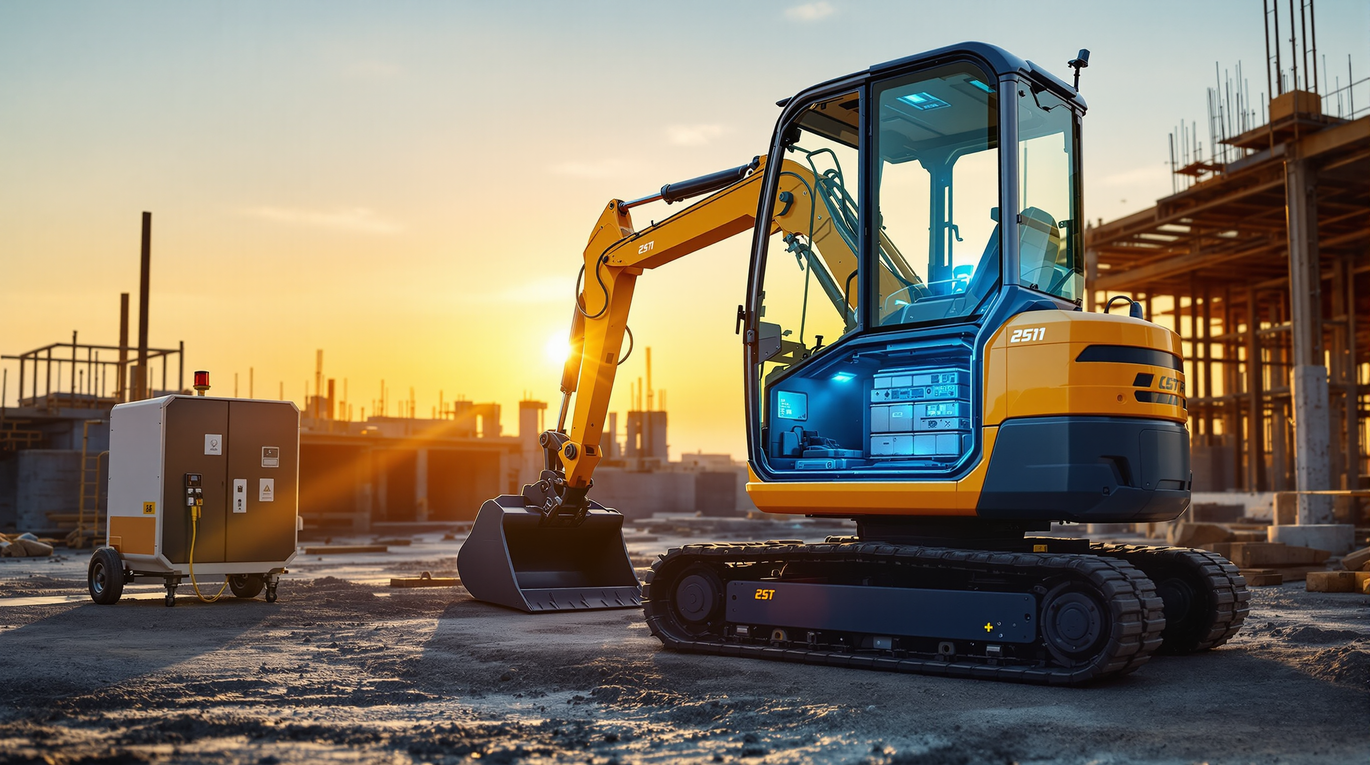
The electric vehicle market continues to expand rapidly due to remarkable advances in battery technology. Experts project this market will exceed $1 trillion by 2029. These changes in the automotive industry have sparked significant developments in compact machinery.
Battery technology has shown exceptional promise for construction equipment. The latest silicon anode batteries can store ten times more lithium ions compared to traditional graphite anodes. This breakthrough benefits compact machinery operations significantly. Equipment powered by these innovative batteries could run longer, and some new cells might extend operational ranges from 310 miles to 547 miles per charge.
Let's examine how these battery developments will revolutionize compact machinery and shape construction operations in 2025.
Current Limitations of Battery Technology in Compact Machinery
Lithium-ion batteries have come a long way, but they still hit some big roadblocks when used in compact construction machinery. These limits make it tough for manufacturers to switch their equipment lineup to electric power. Construction companies face real hurdles as they try to move toward battery-powered options.
Power density challenges in today's lithium-ion batteries
The power density limits of current lithium-ion batteries hold back what compact machinery can do. Today's lithium-ion cells pack only about 0.015 kWh/kg of energy. Even the best lab versions barely reach 400 Wh/kg. This becomes a big deal when construction equipment needs lots of power for heavy tasks.
The balance between power and energy creates another challenge. Energy density tells us how much power a battery stores, while power density shows how fast it can deliver that energy. Construction equipment needs both - steady energy for long runs and quick bursts of power to dig or lift heavy loads.
The basic voltage output of lithium-ion batteries hasn't improved much. The chemistry behind ion movement between graphite and cathode materials hasn't changed much. This affects how well compact machines can deliver steady power throughout their work day.
Runtime constraints affecting productivity
Battery life limits how long compact electric machines can work. Manufacturer data shows these machines typically run 4-8 hours on one charge in "average" use. That's nowhere near what diesel equipment can do.
Several things cut into runtime:
- Heavy-duty tasks like running augers or trenchers can slash runtime by 40-50% compared to basic material moving
- Job sites often lack good charging spots, which makes mid-day charging hard
- Overnight charging takes about 8 hours, leading to long downtimes
Ground testing shows even shorter runtimes than lab results suggest. Machine data shows lots of idle time, though electric systems waste less power during these breaks. In spite of that, limited runtime remains the biggest roadblock to wider use of electric compact machinery.
Weight-to-performance ratio problems
The weight-to-performance balance might be the toughest challenge for battery-powered compact machinery. Battery cooling systems alone can make up 5.4% to 60.4% of a battery module's total weight. This affects how well the machine works overall.
Research shows cutting vehicle weight by 10% can save 3.3-8% in energy use. But keeping enough battery power while dropping weight is sort of hard to get one's arms around for compact machine designers.
Space limits in compact equipment add another layer of complexity. Unlike bigger machines with room to spare, compact equipment has tight space constraints. That's why we see electric mini-excavators and compact loaders before larger machines.
The standard way of using graphite to hold lithium ions adds to the weight issue. Much of the battery's mass doesn't actually store power. This design stops dangerous crystal formations during charging but makes batteries heavier and less energy-dense.
Manufacturers still need to find the sweet spot between battery size, safety features, cooling needs, and weight. This balance is key to building electric alternatives that work as well as their diesel counterparts.
Solid-State Battery Innovation: Game-Changer for Compact Equipment
Solid-state battery breakthroughs will transform the compact equipment industry. These advances tackle the core limitations of traditional lithium-ion technology. The technology swaps liquid electrolytes for solid alternatives, bringing a fundamental change to construction machinery power systems.
How solid-state technology eliminates liquid electrolytes
Solid-state batteries work quite differently from traditional lithium-ion cells. These batteries use solid electrolyte materials instead of flammable liquids. The materials act as both separator and ion transport medium. This design removes the need for graphite anode structures found in regular batteries, so lithium metal builds up right on the anode.
Lithium particles move through the solid electrolyte's atomic structure during charging. They form a pure lithium layer between the separator and the anode's electrical contact. The design creates a smaller anode compared to lithium-ion batteries with graphite structures. This leads to better energy density.
The solid electrolyte, usually ceramic or solid polymer, handles three key tasks at once:
- Acts as the medium for ion transport
- Provides electrical insulation properties
- Serves as a mechanical separator between cathode and anode
Safety improvements for construction environments
Construction sites need batteries that can handle tough conditions. Solid-state batteries excel here because they have no flammable liquid parts. This cuts down fire risks if the battery gets damaged or overheats.
These batteries show remarkable thermal stability. Tests prove that solid-state batteries can handle much higher temperatures before failing compared to standard lithium-ion batteries. The solid electrolyte also fights off dendrites better - those sharp, uneven lithium buildups that often cause short circuits in regular batteries.
The separator layer's ceramic composition with various additives resists high temperatures well. This makes the barrier between anode and cathode more reliable, preventing shorts even under harsh use. The solid-state cells' safety level rises - a crucial factor since construction equipment faces rough handling and extreme conditions.
Extended operational time between charges
Solid-state battery technology packs up to 2-2.5 times more energy than current lithium-ion solutions. This boost comes from removing the graphite anode structure, which results in lighter, more compact batteries that store more power.
Equipment powered by solid-state batteries could run twice as long. This solves a major challenge with today's battery-powered construction equipment. Some solid electrolytes even work better in high temperatures, which helps during fast charging and heavy-duty construction work.
These batteries charge impressively fast - research shows they can charge up to six times faster than current options. While actual speeds vary by design, the basic structure allows for much faster charging rates.
Compact machinery applications already in testing
Companies have started testing solid-state batteries in compact equipment. Small-scale versions work in climate-controlled settings, aerospace uses, and hybrid semi-solid designs.
Dongfeng Motor Corporation in China shows real progress. They launched 50 E70 vehicles using semi-solid-state batteries - a key milestone. Though these first uses focus on vehicles rather than construction equipment, they provide key insights for compact machinery.
Big names like Mercedes, Volkswagen, and Toyota put serious money into developing solid-state technology. Experts think fully ready solid-state batteries for construction could hit the market between 2025-2030, with some makers aiming for 2028 mass production.
The first solid-state batteries will likely power premium compact equipment models. They'll spread to other applications as manufacturing grows and costs drop. Production costs - now much higher than regular batteries - should fall as the technology matures.
Silicon Anode Advancements Boosting Energy Storage
Silicon anodes are changing the game in battery tech. They offer amazing energy storage capabilities for compact construction machinery. Scientists have spent decades in the lab, and now silicon-based anodes are ready for real-world use in heavy-duty equipment.
10x capacity increase over traditional graphite anodes
Silicon's theoretical capacity reaches 3592 mAh/g, which is almost ten times more than graphite's 372 mAh/g. This huge difference comes from silicon's natural ability to store more lithium ions during charging. Graphite needs six carbon atoms to store one lithium ion, while silicon can bond with about four lithium ions per atom.
This amazing capacity comes with its own challenges. Silicon expands up to 300% during lithiation. Scientists have solved this problem through several clever approaches:
- Nanostructuring silicon to handle volume changes without breaking down
- Creating silicon-carbon composites with protective carbon coatings
- Using special binders that keep electrodes intact as volume changes
These breakthroughs let manufacturers boost energy density by 20-40% compared to regular graphite anodes.
Impact on compact excavator performance
Construction teams can get much better performance from their compact machinery with silicon anode technology. Mini-excavators with silicon anodes pack more power without adding extra weight.
Real-world results show these machines can work harder for longer periods. Tests prove that silicon-based batteries keep 88% of their capacity even after 950 cycles. This solves the old problems with durability that construction teams faced.
Reduced charging frequency on construction sites
Construction operations benefit the most from silicon anodes because they don't need charging as often. New silicon anode designs can charge up to 80% in just six minutes.
Quick charging and better energy storage are changing how construction sites use their equipment. The numbers back this up - lithiated silicon anodes keep 73.8% of their capacity even after 1000 cycles at high discharge rates. This means they stay reliable even in tough construction conditions.
The U.S. Army is working on something even better. They want to create silicon-based fast-charge cells that deliver >200 Wh/kg specific energy. These cells should last for more than 1000 cycles at 3C discharge rates while keeping >80% capacity. This research proves silicon's value for heavy-duty applications.
Battery Management Systems Getting Smarter
Modern battery management systems (BMS) now incorporate artificial intelligence and have transformed from simple monitoring devices to smart predictive systems. These advanced systems are vital developments in battery tech that go beyond capacity improvements to focus on operational efficiency and safety.
AI-powered optimization for construction workflows
AI-powered BMS solutions revolutionize construction equipment operations through up-to-the-minute optimization. These systems use neural networks and support vector machines to analyze historical data, driving patterns, and environmental conditions. Machine learning algorithms make more accurate estimations of battery states possible, including charge, health, and power capacity, which are vital for demanding construction workflows.
Smart BMS platforms now automatically adjust parameters based on workload patterns. To cite an instance, when a compact excavator moves from digging to material transport, the system adjusts power distribution to maximize efficiency. Recent implementations show that AI-based systems can extend operational times by optimizing power usage based on task-specific requirements.
Temperature regulation in extreme environments
Thermal management remains a key function of advanced BMS technology. Smart systems use sophisticated temperature regulation techniques to maintain optimal battery performance on construction sites where equipment faces wide temperature variations.
Modern BMS platforms use multiple temperature sensors with AI algorithms to create thermal profiles that predict and prevent overheating. Data shows that temperatures outside the 15-35°C range substantially degrade battery performance. These systems keep temperature differences across the battery pack below 2°C through precise monitoring and control, which is better than conventional systems with variations of 3.6°C or higher.
Predictive maintenance reducing downtime
The most valuable advancement in BMS technology is predictive maintenance capability. AI-powered systems monitor battery performance metrics continuously to forecast potential issues before failures occur, unlike traditional reactive maintenance approaches.
These systems detect subtle indicators of battery degradation such as voltage imbalances or increased connection resistance. Construction operations can schedule maintenance during natural workflow breaks rather than face unexpected equipment failures. One industrial implementation showed substantial reduction in unscheduled downtime through early detection of battery anomalies.
Remote monitoring capabilities now let fleet managers track battery performance across multiple equipment pieces at once. This detailed approach enables proactive maintenance scheduling and reduces operational disruptions while extending battery service life.
Fast-Charging Infrastructure Development for Jobsites
Construction sites need strong charging infrastructure to support battery-powered compact machinery. Companies now blend electric equipment into their fleets. New charging solutions have emerged to handle the unique challenges at construction sites.
Portable charging solutions for remote locations
Construction sites' mobility needs have led to versatile charging units. The PU750 mobile charging unit charges mid-size electric machines on various jobsites. It adapts to different setups and moves easily on a lowboy trailer. The compact PU130 works as a portable AC and DC fast charger that fills smaller machines in under an hour.
The PU40 power unit brings charging capabilities anywhere with its 40kWh capacity. This works even at sites that have minimal grid connection. The 900kg unit can power up Volvo compact electric excavators within an hour. Compact wheel loaders take two hours to charge. These solutions work with non-Volvo machines and other electrical equipment.
Solar-powered options reducing grid dependency
Beam solar fast chargers offer standalone solar charging capabilities. Their solar panels track the sun's position automatically to capture maximum energy. Each unit comes with two North American Type 1 charging plugs. They match standard 240-volt setups with 6-hour charging times while running completely off-grid.
Solar solutions create operational benefits beyond cutting emissions. Battery-electric hybrid systems reduce generator service visits from every 1-2 weeks to once every 2 months. Diesel engine runtime drops by up to 83%.
Standardization efforts across equipment manufacturers
The industry moves toward standardization through shared initiatives. Volvo Construction Equipment released its brand-agnostic 48V DC fast charging protocol. This open approach creates compatibility between brands. It addresses customer concerns about needing multiple chargers for different equipment brands.
The American Rental Association and Association of Equipment Management Professionals now work together on charging specifications. Their proposal suggests three standard scenarios: EV-style fast charging, mobile charging with adapters, and on-site charging with standard power connections.
Conclusion
Battery technology breakthroughs will transform how compact machinery operates in 2025 and beyond. Solid-state batteries offer doubled operational range and better safety features that solve many problems which limited electric equipment adoption. Silicon anode innovations now provide high-capacity storage essential for construction tasks.
AI-powered battery management systems can predict when maintenance is needed before issues occur. This technology substantially cuts down unexpected downtime. The combination with new fast-charging infrastructure makes battery-powered equipment a practical choice for construction sites.
The construction industry is moving toward widespread electrification despite some obstacles. Standardization and remote charging capabilities need work. Companies that invest in these technologies now will likely see major returns as battery-powered machinery becomes standard practice instead of an exception.