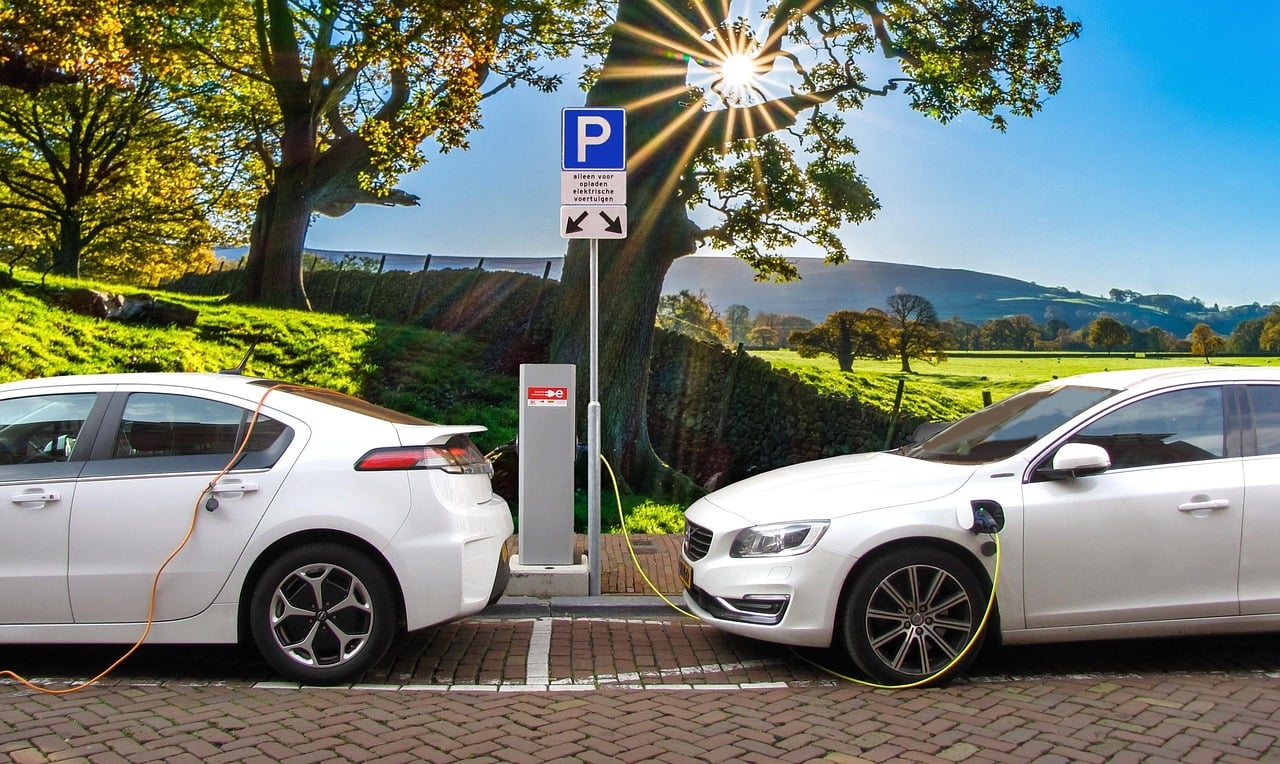
The numbers tell a clear story - electric equipment costs $17,073 less to operate annually than traditional hydraulic systems. Most people think hybrid versus electric choices only matter for cars and vehicles. The reality shows this decision affects equipment of all types.
Electric options are becoming more popular throughout the industry. Companies like Loxam now secure green loans worth millions, and many buyers willingly pay 25% extra for zero-emission machines. The choice involves more than just comparing purchase prices. Electric machines run with 300 fewer moving parts than hydraulic versions. Plus, battery costs have dropped 33% since 2022, which makes the financial picture change faster every day.
This piece breaks down what hybrid and electric equipment will really cost in 2025. You'll learn enough to make smart choices that work for your budget and operations.
The True Cost of Ownership: Beyond the Price Tag
Equipment costs involve more than just the price tag. Market analysis shows major changes in financial patterns between hybrid and electric machinery in 2025.
Original purchase price differences in 2025
The Department of Energy's latest analysis reveals electric equipment has higher upfront costs. A typical electric commercial vehicle costs $30,000 more than regular models. Battery costs have dropped remarkably from $150/kWh to $128-133/kWh for light-duty equipment. Manufacturers now offer hybrid options at better prices, which cost 25% less than fully electric alternatives.
Hidden costs that affect your bottom line
Several mechanisms influence total ownership expenses beyond your first investment. Electric equipment needs special charging infrastructure, and a Level 2 charging station costs about $1,200 to install. The maintenance patterns vary between technologies. Electric machines show 50% lower maintenance costs throughout their lifespan because they have fewer moving parts and simpler mechanical systems.
Operating costs are a vital consideration. Electric equipment owners save $100 monthly on fuel and maintenance combined. Businesses that use more than 100 gallons of fuel monthly can save up to $400 by switching to electric.
Depreciation rates: hybrid vs electric
The most notable differences show up in depreciation patterns. Electric equipment loses value faster, dropping about 50% of its original worth in five years. Hybrid machinery holds its value better, with a five-year depreciation rate of 37.4%.
These value differences become clearer in specific cases:
- Electric vehicles depreciate at $0.27 per mile compared to $0.11 for conventional equipment
- Hybrid equipment has the second-best depreciation rate across all vehicle classes, beaten only by specialized equipment like pickup trucks
- Battery-electric models keep 26% of their original value after 100,000 miles, while hybrids maintain 31%
Market dynamics change faster now. Battery costs keep falling, showing a 33% drop between March 2022 and August 2023. Electric equipment's maintenance savings grow over time, with expected savings of $2,743 over 100,000 miles of operation.
Experts see more cost reductions ahead. Hybrid system costs should drop to half their 2010 levels by 2025. Battery technology improvements and increased production will reduce electric equipment expenses as manufacturers produce more units.
Operational Costs Breakdown: Fuel vs Charging
The economic landscape of 2025 shows significant differences in operational costs between hybrid and electric equipment. Fuel and charging expenses play a vital role in purchase decisions, and recent data highlights these differences clearly.
Average energy costs per mile/hour of operation
Electric equipment shows remarkable efficiency in daily operations. Electric vehicles cost about $0.05 per mile to operate, which is a big deal as it means that conventional options cost more at $0.13 per mile. American equipment owners typically drive 14,263 miles each year. This translates to energy costs of $998 for electric equipment owners, while $2,425 goes to traditional fuel-powered machinery.
Location affects actual savings for businesses operating across different states. Operators in Washington state can save $80 per full charge cycle thanks to favorable electricity rates. The story changes in California, where operational costs rise to $0.09 per mile.
Charging infrastructure expenses for electric equipment
Smart planning helps balance immediate and long-term costs of charging infrastructure. Level 2 charging stations are vital for smooth operations and cost between $2,000 to $5,000 per unit. Installation adds $500 to $2,000 depending on existing electrical setup.
Charging equipment needs regular upkeep:
- Each charger needs $400 yearly for maintenance
- DC fast chargers' extended warranties cost over $800 per year
- Monthly network connectivity fees run $30-100 for each charging port
Fuel price projections through 2025
Electric equipment maintains its cost advantages in future projections. The Energy Information Administration expects gas prices to drop by 11 cents per gallon in 2025, with another 18-cent decrease in 2026. Analysts predict average gas prices will hover around $3.22 per gallon throughout 2025.
Electric charging stays cheaper despite falling fuel prices. Most regions will see stable electricity rates with minimal changes. Smart operators can cut costs by 20-30% using time-of-use rates and special EV charging programs during off-peak hours.
Electricity prices remain stable while fuel markets fluctuate. Gas prices trend downward but global market conditions cause ongoing changes. Fleet operators benefit from predictable electricity costs which makes budget planning easier.
Maintenance Expenses: What the Dealers Don't Tell You
Equipment dealers often avoid talking about the real story behind maintenance costs that lurks beneath their shiny brochures and sales talks. New maintenance data shows some eye-opening facts about what hybrid and electric machinery really costs to own long-term.
Battery replacement timelines and costs
Hybrid and electric equipment show big differences in how long their batteries last. Electric vehicle batteries usually work for 8-10 years before you need a new one, with replacement costs between $5,000 and $20,000 based on size and brand. Battery prices keep dropping, and right now they average $111/kWh in 2024.
Hybrid equipment batteries need replacement after 80,000 to 100,000 miles. You'll pay between $1,000 and $6,000, which costs much less than electric equipment batteries. Third-party companies now make compatible replacement batteries that cost 30-40% less than original manufacturer parts.
Hybrid system maintenance requirements
Hybrid systems need more regular care because they use two power systems. Regular maintenance tasks include:
- Oil changes every 30,000 to 50,000 miles at $128 to $142
- Tire rotations every 5,000 to 8,000 miles at $35 to $44
- Brake pad replacements every 10,000 to 20,000 miles at $230 to $274 per pad
Working on hybrid systems takes special technical knowledge. These machines have about 2,000 moving parts because they combine electric and combustion components, making them much harder to service than pure electric options.
Repair frequency comparison
Electric equipment breaks down less often. Only 1.5% of electric vehicles need battery replacements outside their warranty. These machines need half the maintenance of regular equipment because they only have 20 moving parts instead of a hybrid's 2,000.
The cost difference grows larger over time. Electric equipment owners pay about $900 yearly for maintenance, while hybrid owners pay $1,200. Electric systems don't need oil changes, transmission services, or frequent brake repairs, which explains this difference.
Some electric equipment repairs can be trickier to fix. The lack of qualified technicians and complex high-voltage systems mean repairs take longer. Accident repairs for electric equipment also cost more because they need special parts and safety measures.
The future looks brighter for maintenance costs of both types. Battery costs should drop by 70%, which could make replacements much cheaper. As more technicians learn to work with these technologies, labor costs should level out, making repairs more available and affordable for everyone who owns hybrid or electric equipment.
Tax Incentives and Rebates in 2025
Tax incentives and rebates in 2025 are changing how businesses look at hybrid and electric equipment investments. These programs can help you offset your upfront costs and boost your returns over time.
Federal incentives for electric equipment
Starting January 1, 2025, businesses that buy new electric vehicles and equipment can get major federal tax credits. Vehicles under 14,000 pounds qualify for credits up to $7,500. Heavy equipment above this weight can receive credits up to $40,000. The credit amount equals whichever is less:
- 15% of what you pay for plug-in hybrid equipment
- 30% of what you pay for fully electric equipment
Businesses can also claim tax credits for charging infrastructure worth 6% of their costs, maxing out at $100,000 per charging unit. Companies that meet wage requirements might get bigger credits covering 30% of their expenses.
State and local rebate programs
State programs in 2025 add even more value on top of federal incentives. The Home Energy Rebate (HEAR) Program gives rebates up to:
- $8,000 when you install heat pumps
- $4,000 for electric load service center upgrades
- $2,500 for electrical wiring changes
Utility companies in all 50 states now give special rebates and better rates when you switch to electric equipment. Pacific Gas & Electric leads this trend by offering infrastructure upgrade rebates that target construction industry fleets.
Business tax advantages for green equipment
The commercial clean vehicle credit creates amazing opportunities for businesses in 2025. Your organization can claim credits for:
- Mobile machinery and construction equipment
- Fleet vehicles used in trade operations
- Charging infrastructure installations
These business credits stand out because they don't have many of the limits that consumer incentives do. Business claims skip past these common restrictions:
- North American assembly requirements
- Income limitations
- Manufacturer suggested retail price caps
Your business can stack multiple incentive programs to maximize savings. You can use all these at once:
- Federal tax credits for equipment purchases
- State-level rebates for infrastructure
- Utility company incentives for operational costs
Tax-exempt organizations can now get these benefits through direct pay provisions. Non-profit groups receive payments straight from the IRS when they meet the credit requirements.
ROI Timeline: When Each Option Pays for Itself
You need to analyze carefully when hybrid and electric equipment starts paying off to make a smart choice between them. Market data gives us a clear picture of break-even timelines for different types of equipment.
Break-even point analysis for different equipment types
Electric options in compact equipment give you the quickest return on investment. Small electric vehicles take 3-7 years to break even for 200-mile range models. Larger 300-mile range equipment needs 9-20 years to reach cost parity.
The financial story looks quite different for hybrid machinery. The data shows hybrid equipment needs about 7 years of regular use before savings cover the original investment premium. This timeline gets shorter in areas with expensive fuel and cheap electricity.
Usage volume impact on ROI
The amount of equipment use plays a huge role in return on investment calculations. Electric machinery works best financially when used more often. The break-even points speed up as daily operating hours go up.
ROI patterns vary by equipment type:
- Light-duty electric equipment becomes profitable at 1.7 hours daily use
- Medium-duty machinery needs 7.5 hours daily operation
- Heavy-duty equipment needs over 8 hours daily use
Hybrid equipment shows more stable ROI patterns no matter how much you use it. Research shows hybrid machinery cuts emissions by 35-40% at any usage level, which leads to steady savings.
Resale value projections
The resale picture toward 2025 looks interesting. Electric equipment keeps about 43% of its value after five years. Hybrid machinery does better by keeping nearly 69% of its original worth over the same time.
The difference really shows up in specific areas:
- Commercial electric vehicles keep 45.56% value after 5 years
- Hybrid equipment holds 68.92% residual value
- Traditional equipment averages 65.09% retention
The market right now favors hybrid options if you want returns sooner. Electric equipment makes more financial sense over longer periods, especially if you run operations more than 8 hours daily. Your choice should match how much you plan to use the equipment and your investment timeline to get the best returns.
Conclusion
You just need to think over many factors when choosing between hybrid and electric equipment. Electric options cost more upfront, but they save you $17,073 every year in running costs. This makes them a smart choice if you plan to use them for many years.
The market has changed a lot. Battery costs dropped 33% since 2022. Hybrid equipment still holds its value better and keeps 69% of its worth after five years. Electric machines are affordable when used more than 8 hours daily. Hybrid options give you faster returns if you use them less often.
Heavy equipment buyers can get federal tax credits up to $40,000. State rebates and utility incentives help cut down the original costs by a lot. Electric options also need 50% less maintenance because they have fewer moving parts.
Your specific needs and timeline will help you make the right choice. Electric equipment works best for heavy usage and long-term ownership. Hybrid options are great for businesses that want quick returns and better resale values.