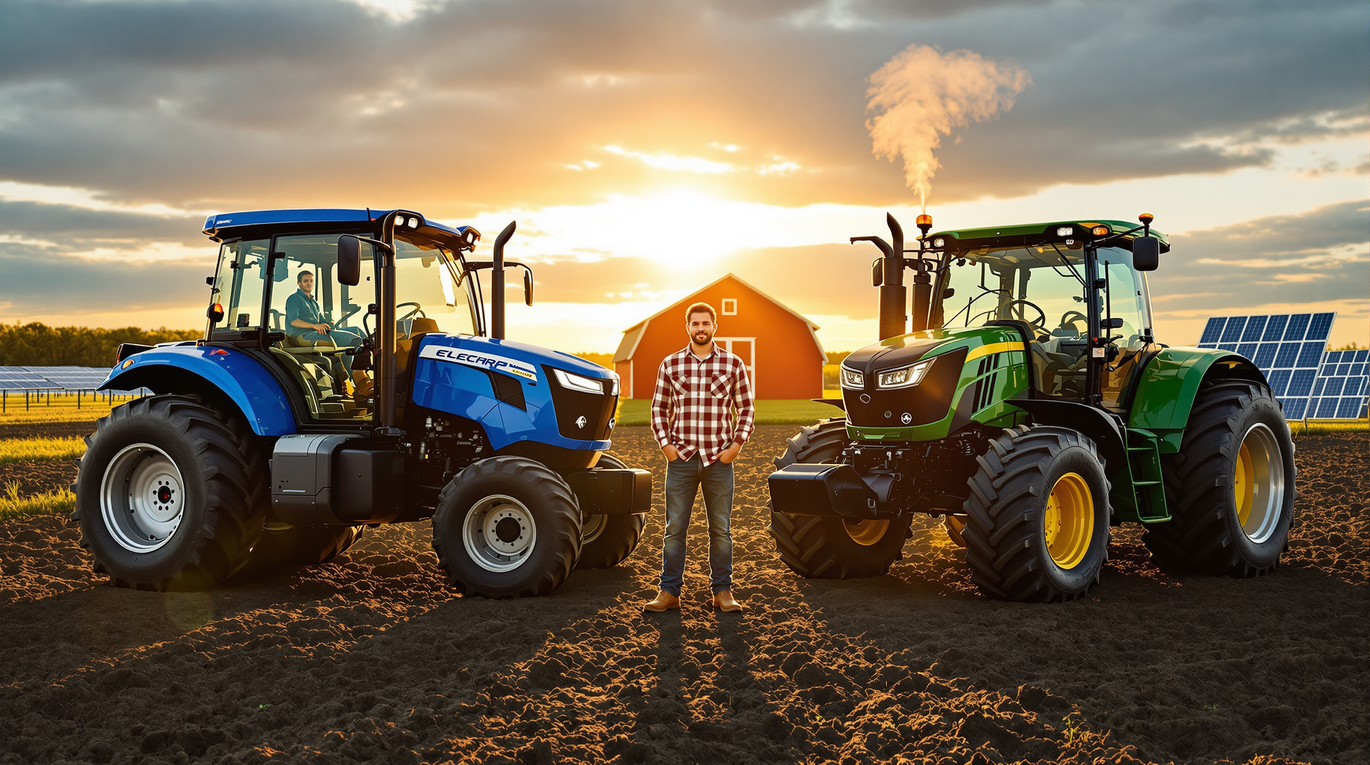
China's 22 million agricultural tractors add by a lot to pollution. Small tractors make up 17.3 million of this massive fleet. Farmers worldwide now face mounting pressure to cut their emissions, which makes the choice between diesel and electric tractors more crucial than ever.
Diesel electric hybrid tractors (DHT) deliver remarkable environmental benefits, though they cost more upfront. Studies show that electric equipment can slash emissions by up to 95% compared to traditional diesel models. Manufacturers proudly share these impressive numbers, but many farmers still hesitate to make the switch. Our extensive research reveals real-life experiences that farmers rarely share about both diesel and electric tractors.
The Real Performance Gap Between Electric and Diesel Tractors
The ground performance of electric tractors shows big differences from diesel models that go beyond what manufacturers claim. Farmers must learn these differences before switching to alternative power sources.
Power output in challenging conditions
Electric tractors deliver full torque instantly, unlike diesel engines that take time to reach their best power levels. This makes electric tractors work better for tasks that need precise control. In spite of that, today's battery tech can't sustain high power output. Electric tractors work best with light loads under 20%, while diesel tractors shine in heavy-duty jobs that need constant high torque.
John Deere's diesel electric tractor models keep performing well even on tough terrain. Their hybrid systems blend diesel efficiency with electric responsiveness. On top of that, modern diesel tractors usually provide 300-600 hp for long periods. Pure electric models can't match this power when they face tough soil conditions or need to run longer.
Battery life vs. fuel tank capacity
Diesel fuel packs way more energy than batteries, which creates the most important operational gap. A standard diesel tractor can run for 16+ hours on one tank, while electric tractors run between 3-14 hours based on workload and conditions. A diesel tractor takes minutes to refuel, but batteries need several hours to recharge.
A 400-gallon diesel tank would need 67,000 pounds of batteries to match its energy - that's 20,000 pounds heavier than the tractor itself. The Fendt e100 Vario can charge to 80% in 40 minutes, but this still limits work during vital planting or harvest times.
Electric tractors must return to charging stations often, which cuts their field time. Rural power grids usually can't charge multiple large tractors faster at once. These limits explain why hybrid models have become popular for medium-duty farming - they offer a practical middle ground.
Weight and maneuverability differences
Battery packs are heavy, which brings both good and bad points. One manufacturer says, "The biggest problem with electric cars is the weight of the batteries. I realized very quickly that weight on a tractor is actually an asset that improves traction". This extra weight can help with traction sometimes.
Heavy electric tractors might pack the soil too much, which hurts soil health and crop yields. Their weight affects how well they move, especially in wet conditions where they might get stuck. Today's electric tractors weigh 30-50% more than diesel ones. They need stronger frames and special parts to handle this extra weight.
Actual field efficiency comparisons
Tests in the field show interesting patterns. Electric tractors with active torque-distribution control cut slip by 14.83% and made traction 10.28% better than regular methods. The joint control method for traction and ballast used 4.9% less energy in drive motors.
Money-wise, electric tractors are 84.86% more cost-efficient than diesel ones for energy use. Diesel tractors cost about $93.50/km to run, while electric ones cost $14.15/km.
Electric tractors work better for light jobs, but diesel or hybrid options make more sense for heavy, ongoing work. This gap keeps getting smaller as tech improves, but practical limits still exist for the toughest farm jobs.
Hidden Operational Challenges of Electric Farm Equipment
Electric tractors face real-world challenges that you won't find in sales brochures. These practical issues can make the difference between a valuable farm asset and a costly mistake.
Charging infrastructure in rural areas
Rural charging infrastructure poses the biggest roadblock for electric farm equipment adoption. About 20% of Americans live in rural areas with almost 70% of America's lane miles, but these regions lack strong electrical infrastructure. Electric tractors need substantial charging capacity, which creates a major barrier.
Power supply in rural grids isn't reliable, and outages happen often. Even areas with steady power have grids that can't handle the extra load from widespread electric vehicle use. This means farmers might not be able to charge their tractors when they need to, or they'll pay too much to do it.
The problem gets worse because rural operations spread out over large areas. Unlike cities, farms have big distances between work sites. Setting up charging stations at every field location costs too much and isn't practical. Farmers using John Deere diesel electric tractors or regular diesel equipment don't have these limits, which gives traditional options a clear advantage.
Weather impact on battery performance
Temperature swings affect electric tractors in ways that diesel equipment doesn't experience. The North American Council for Freight Efficiency's research shows electric vehicle range drops by about 10 percent for every 10 degrees Fahrenheit below 30 degrees. This happens because lithium ions in batteries move slower in cold weather, making the battery less effective.
Cold weather creates two energy problems for electric tractors. The battery system needs power to stay at the right temperature while also heating the cab. This leaves less energy for actual work - a big problem during crucial times like planting or harvesting.
Hot weather brings its own set of issues. High temperatures can cause problems with heat management and reduce the tractor's efficiency. Regular diesel electric tractors handle heat better through traditional cooling systems, while electric models must balance cooling needs with power saving.
Humidity and dust make things more complicated. Condensation from high humidity might cause short circuits, and dust can clog cooling systems. These environmental factors add uncertainty that farmers must think about when choosing between diesel and electric tractors.
Emergency power solutions
New solutions are coming up to tackle power challenges. The California Energy Commission gave $3 million to a group including Monarch Tractor to show how "Vehicle-to-Building Technologies for Resilient Backup Power" works. This technology lets electric tractors work as mobile power sources during blackouts.
Gridtractor's Rural Electrification And Charging Technology (REACT) program helps farmers get incentives for charging systems to offset infrastructure costs. Some farmers now use solar-powered charging stations for self-sufficient energy. One farmer uses 1,200 watts of solar panels to power an 8 kWh battery bank that charges their electric tractor completely off-grid.
Diesel electric hybrid tractors offer a middle ground for farmers who aren't ready to go fully electric. These systems provide backup power during outages while helping the environment. Special generator circuit breakers like the NZMN2-VE250 help tractors safely power essential farm operations when the grid fails.
Maintenance Realities: What the Brochures Don't Tell You
The fine print hides many maintenance details when you compare diesel and electric tractors. These details greatly affect how satisfied owners feel in the long run. What manufacturers happily showcase in glossy brochures rarely shows the real-world challenges of keeping these machines running.
Specialized technician availability
Finding qualified technicians is one of the biggest challenges of owning an electric tractor. Rural areas—where most farms operate—don't have enough mechanics trained to work on advanced electric systems. The agricultural equipment service industry needs technicians with specific training in computer technology, electronically controlled hydraulics, and navigational electronics.
Diesel tractors benefit from a network of experienced technicians built over many years. Farm equipment mechanics earn a median annual wage of $49,210, and experienced technicians can make up to $72,450. Electric tractor technicians need even more specialized knowledge and command higher pay, which makes the shortage worse.
One industry observer said, "The days of working on your equipment with only simple hand tools are a thing of the past". This rings especially true for electric tractors because high-voltage systems need extra safety training and certification. Farmers who usually fix their own equipment often find they don't know enough to diagnose and repair electric systems.
Rural areas lose skilled workers to cities where opportunities are better. This brain drain leaves behind technicians who might not have the advanced electrical training needed for sophisticated e-tractors.
Parts accessibility and costs
E-tractor owners struggle with parts availability. Solectrac owners learned this the hard way when they couldn't use their equipment after the company shut down. Without established dealer networks nearby, getting replacement parts takes longer and costs more to ship.
Parts availability matters for both diesel and electric tractors. Notwithstanding that, diesel tractors benefit from decades of standardization and widespread parts networks. Electric tractor parts often must come directly from manufacturers, sometimes from overseas.
Replacing batteries costs e-tractor owners a lot of money. These power units need replacement every 7-10 years - a major expense diesel tractors don't have. Specialized electric parts also cost more because of limited production and unique designs.
Diagnostic equipment requirements
Today's tractors need specialized diagnostic tools that cost a lot. Electronic Diagnostic Tool (EST) software licenses range from $300 for single product series to $1,500 yearly for all products. Complete repair work needs Electronic Technical Information Manuals (eTIM) that cost $2,495 yearly.
These costs add up with more hardware needs:
- Engine-specific diagnostic tools: $400-$1,200 depending on manufacturer
- Diagnostic interfaces: $1,100-$1,900
- Complete diagnostic kits with software: $3,800-$4,100
The right-to-repair movement matters even more with electric tractors. Manufacturers control access to diagnostic information, which limits farmers' repair options. The switch to electronic systems gives manufacturers and dealers more control, reducing farmers' freedom to make maintenance decisions.
Electric tractors need less maintenance than diesel ones because they have fewer moving parts. Yet, they depend heavily on specialized diagnostic equipment, which creates a financial rather than mechanical burden.
Diesel Electric Hybrid Tractors: The Overlooked Middle Ground
A pragmatic alternative exists between pure electric and conventional diesel tractors that farmers often overlook: diesel electric hybrid tractors. These machines strike a perfect balance of performance, efficiency, and practicality in modern agriculture.
How John Deere diesel electric tractor models perform
John Deere's diesel electric tractors employ an Electric Variable Transmission (EVT) instead of traditional mechanical transmissions. This state-of-the-art design provides infinite speed control and faster acceleration through its stepless operation. The 644 X-Tier (previously 644K Hybrid) and 944 X-Tier have proven their reliability with over 3 million customer hours in the field.
These hybrid models deliver exceptional torque response while handling load fluctuations. The electric motors cut engine torque ripple by 34.1% compared to conventional single-engine tractors. Smoother operation in variable field conditions substantially extends the engine's service life.
Real-life fuel savings data
Recent studies present compelling evidence for diesel electric hybrid tractors' economic benefits. These hybrid systems reduce total energy costs by 9.42% during plowing operations. Testing shows hybrid tractor architecture improves energy consumption economy by 6.2% over rule-based systems in conventional plowing conditions.
STEYR's research demonstrates fuel consumption advantages of 8% with their Hybrid Drivetrain Konzept. The most impressive results emerge from specific operations - e-PTO hybrid architecture saves up to 16% fuel in low-demanding tasks.
Adaptability to farming operations of all types
Diesel electric hybrid tractors' flexibility stands as their greatest asset. These machines work efficiently in various modes including plowing, rotary tillage, and transportation. John Deere's larger 8 and 9 series tractors now offer EVT options, giving farmers electrification benefits without compromising operational range.
Model Predictive Control (MPC) systems in hybrid tractors optimize power distribution between the diesel engine and electric motor. This optimization balances energy efficiency and NOx emissions based on workload needs. The adaptive system keeps the diesel engine running at peak efficiency whatever the application.
Field testing proves diesel electric hybrids excel especially with medium-duty farming tasks where engine loads stay between 20% and 60%. Farmers looking to improve efficiency without fully electric equipment's constraints will find these tractors are a great solution.
Regional Factors Affecting Electric vs Diesel Tractor Viability
A farm's location plays a key role in determining which tractor technology makes financial sense. Different regions create unique operating conditions that can make electric tractors either a smart investment or an expensive mistake.
Climate considerations
Cold and hot weather affects electric tractor performance differently than diesel equipment. Battery range drops about 10 percent for every 10 degrees Fahrenheit below 30 degrees. This happens because lithium-ion batteries don't work well in cold weather, and farmers need extra power to keep the batteries at the right temperature.
Diesel electric tractors work reliably no matter the temperature. These tractors have shown better results in mountainous areas, which make up 25% of global land and house 10% of people worldwide. The diesel electric hybrids save 6.2% more energy than standard systems in these regions.
Distance to service centers
Most farms are located nowhere near qualified electric vehicle technicians. Finding mechanics who know how to fix advanced electric systems is already tough in the agricultural equipment industry. Farmers might face long delays waiting for specialized repairs when their electric tractors break down.
Charging infrastructure creates another challenge for remote operations. Rural areas house 20% of Americans and contain almost 70% of America's roads, but they lack proper electrical infrastructure. This makes diesel tractors or diesel electric hybrids a more practical choice for farms away from cities.
Local incentives and regulations
Government programs can substantially change the cost differences between tractor types. Farmers can get up to 50% of their renewable energy project costs covered through the Rural Energy for America Program. The Environmental Quality Incentives Program (EQIP) helps pay for equipment that benefits the environment.
Tax rates also affect buying decisions. Electric tractors, including other vehicles, face only 5% tax rates in some areas compared to 12% for diesel models. This creates big savings upfront.
Benefits change a lot based on location. Oregon wants to add electric tractors to their vehicle rebate programs. The Biden administration has also set stricter emissions rules for trucks and tractors that will speed up the switch to electric options.
Conclusion
Electric tractors provide significant environmental advantages, but practical limitations still hold back their adoption. These machines cut emissions by up to 95% compared to diesel models. The biggest challenges include charging infrastructure, battery life, and maintenance needs that need careful review.
Diesel electric hybrid tractors have emerged as a practical solution for farmers. These machines combine diesel power's reliability with electric efficiency to deliver steady performance in a variety of farming conditions. Tests in actual fields show fuel savings of 8-16%. This makes them an attractive choice for operations looking to move toward cleaner technology step by step.
A farm's individual circumstances heavily influence smart tractor selection. Weather conditions, proximity to service centers, and local incentives are vital factors that determine the best power source for specific agricultural needs. Farmers should review their operational requirements, regional infrastructure, and support systems before they commit to any technology.
The choice between electric and diesel isn't black and white - it depends on your farm's needs and capabilities. Technology improves faster each day, and today's best solution might change as infrastructure grows and battery technology advances.