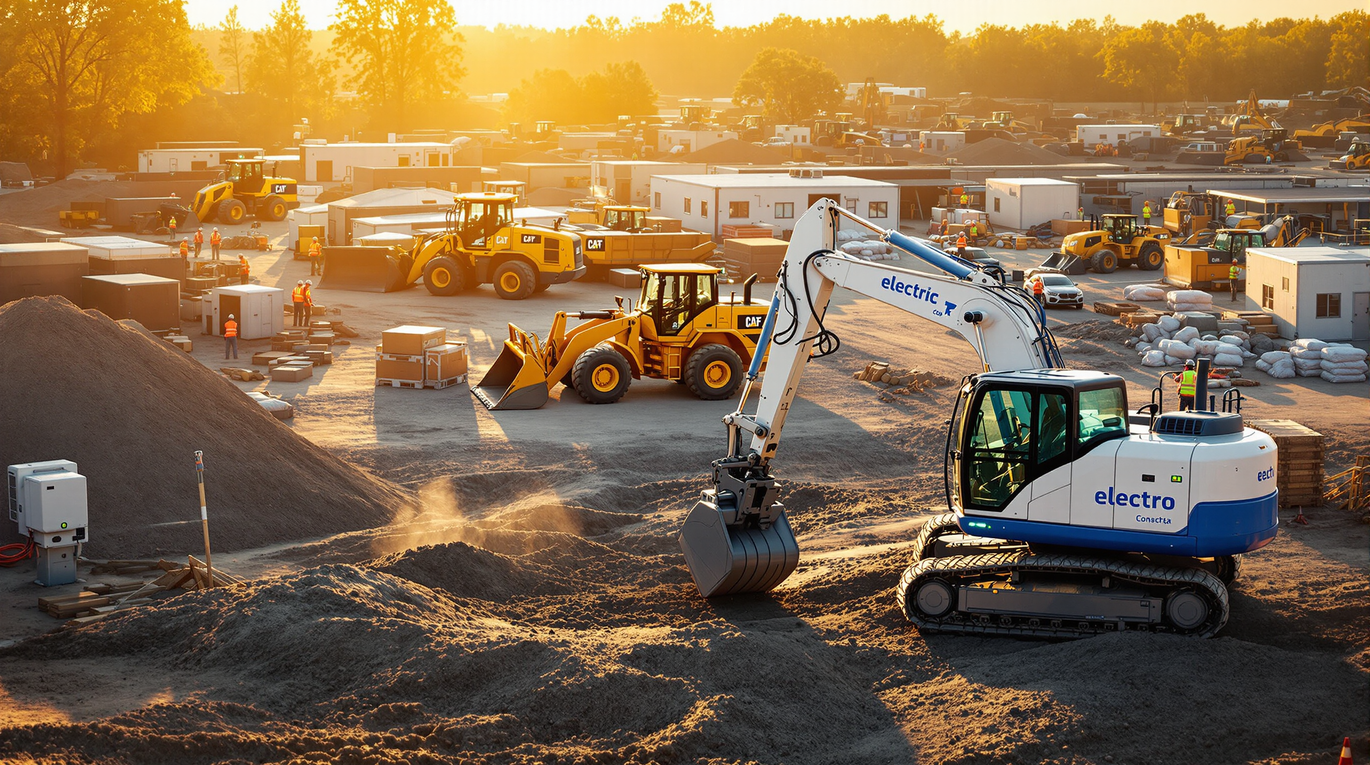
The construction industry leaves a massive environmental footprint. Global energy consumption stands at 36%, while greenhouse gas emissions reach 37%. Construction equipment electrification now revolutionizes these statistics, and industry leaders like Volvo plan to make electric machines 35% of their sales by 2030.
The electric construction equipment market shows remarkable growth potential. Experts project it to reach $126 billion by 2044. Green construction equipment continues to gain momentum despite cost differences. An electric mini excavator's price tag of $66,000 exceeds its diesel counterpart by $40,000. This piece explores why electric construction vehicles are becoming the new standard and guides businesses through this transformation.
The Economic Case for Electric Construction Equipment
Electric construction vehicles offer impressive benefits like zero emissions and quieter operations. The economics behind construction equipment electrification makes it a compelling choice. These machines prove to be sound investments that substantially reduce costs over time.
Lower operational costs over equipment lifetime
Electric construction equipment dramatically cuts day-to-day operating costs. The cost of electricity is nowhere near that of diesel, which leads to huge savings throughout a machine's life.
A standard 20-ton excavator uses about 13,000 liters of diesel each year—costing around $13,000 at global average prices. The cost to charge an equivalent electric machine runs just $6,690 annually (using $0.15/kWh). Machine owners can save up to $75,000 over their equipment's service life.
European operators see even bigger savings. Diesel costs about $2.00/L and electricity averages $0.30/kWh there. A 20-ton electric excavator saves operators $12,620 each year compared to diesel models.
Electric machines also turn off automatically when idle. This feature eliminates the running hours that diesel machines need to keep fuel and fluids moving. The reduced operating hours boost resale value and lower the total cost of ownership.
Reduced maintenance requirements and expenses
The maintenance needs of electric construction equipment are substantially lower than traditional machinery. These machines don't need complex combustion engine parts, which cuts maintenance costs by up to 50%.
A 20-ton excavator's owner saves nearly $15,000 in maintenance over its lifetime. Small machines like 3-ton mini-excavators save almost as much on maintenance as they do on fuel.
Electric equipment's maintenance advantages include:
- Electric motors that need no maintenance and shut off automatically
- Electric drivelines that cut hydraulic oil needs in half
- No oil, air, or fuel filters needed
- No engine coolant, radiators, thermostats, fuel sensors, injectors, belts or alternators required
- Lithium-ion batteries that need no maintenance
Volvo Construction Equipment's data shows users spend 35% less time and money on maintenance over their electric machines' lifespans.
Available tax incentives and government subsidies
The Inflation Reduction Act's IRC Section 45W offers substantial tax credits to companies that buy clean vehicles before January 1, 2033. Fully electric construction equipment qualifies for a 30% tax credit on the purchase price. The maximum credit is $7,500 for vehicles under 14,000 pounds and $40,000 for heavier equipment.
State programs add more savings. California's Clean Off-Road Equipment Voucher Incentive Project (CORE) gives point-of-sale discounts up to $500,000 per voucher for zero-emission off-road equipment.
Local utilities like Pacific Gas & Electric (PG&E) help offset infrastructure upgrade costs through fleet vehicle rebates.
ROI timeline for different equipment types
The biggest challenge with electric construction equipment remains its higher upfront cost—40-100% more than diesel versions. Battery costs (around $300/kWh) and manufacturer R&D investments drive this premium.
In spite of that, most electric construction equipment pays for itself during its operational lifetime through combined savings from fuel, maintenance, and incentives. Small equipment like mini-excavators and compact loaders reach breakeven faster than larger machines because maintenance savings make up a bigger part of their total cost reductions.
Machine utilization, local energy prices, and whether it's a purpose-built electric or updated diesel model affect ROI calculations. IDTechEx research suggests the price premium will eventually match just the battery pack cost as production increases, which will speed up ROI timelines.
Major Players Driving the Electric Equipment Revolution
The competition to develop battery-powered construction equipment has picked up speed over the last several years. Major manufacturers are not just meeting market needs but actively shaping construction's future through innovative electric solutions.
Leading manufacturers and their flagship models
Volvo Construction Equipment leads the construction equipment electrification race with the industry's largest lineup of electric heavy equipment. Their collection has electric mini excavators, wheel loaders, an asphalt compactor, and the 23-ton EC230 Electric excavator. This midsize excavator proved its value on jobsites by reducing hourly carbon emissions by 66% and hourly costs by 74% during a 90-day test with Skanska.
Caterpillar showed four electric prototypes in late 2022, including the 301.9 mini excavator and 950 GC medium wheel loader. These machines run on Cat's own battery prototypes with onboard AC chargers, showing their commitment to sustainability.
JCB's E-TECH range features the award-winning 19C-1E mini excavator—the first fully electric mini excavator in the industry. Their lineup also has the 505-20E telehandler, HTD-5E dumpster, and electric site dumpers that use maintenance-free lithium-ion batteries.
Komatsu's journey with alternative fuel options started in the 1950s. They showed several zero-emission prototypes recently, from the PC01E micro excavator to the 20-ton PC210E. Their work with Honda created innovative battery solutions for their smallest machines.
Rental companies expanding electric fleets
Rental companies are a vital part of making electric construction equipment available to more people without high upfront costs.
Sunbelt Rentals jumped ahead by receiving the first delivery of Bobcat's T7X all-electric compact track loaders in September 2022. This partnership shows how rental fleets help prove new electric technologies.
United Rentals has grown its electric options. They offer various battery-powered excavators, loaders, and other equipment through more than 1,300 locations. Their size helps contractors of all types test these machines before buying.
Rental companies have become valuable advisors for contractors switching to electric fleets. They understand charging infrastructure and runtime management better than most.
Innovative startups disrupting the market
New companies bring fresh ideas to the electric equipment market. Viridi Parente raised nearly $100 million to speed up production of lithium-ion battery systems for construction equipment. Their Green Machine systems power excavators and other machines, while their Volta systems store energy for different uses.
First Green Industries (formerly Kovaco Electric) sells the Elise 900, the first full-sized electric skid steer loader. It runs for 8 hours with their 400Ah battery system and offers remote operation.
Chinese manufacturers make their mark too. LiuGong has over 2,000 electric wheel loaders working worldwide, while Yuchai Heavy Industry launched what they call the largest tonnage electric skid steer loader available.
These market changes show a transformation in construction equipment design. Battery technology keeps improving and production increases, moving the industry toward what a world of zero-emission equipment looks like - the new standard rather than the exception.
Real-World Performance of Battery Powered Construction Equipment
Many engineers and contractors ask if battery powered construction equipment can match what traditional diesel machines can do. The answer lies in field tests and ground applications that now give us clear proof.
Comparing work output to traditional diesel equipment
Leading manufacturers' battery-powered excavators and loaders have showed performance specs that are similar to their diesel counterparts. The Volvo ECR25 electric excavator packs slightly more continuous motor power with just a bit more operating weight than its diesel version. Operators in field tests say electric machines feel stronger than diesel ones. The instant torque from electric motors eliminates the usual delay you get with diesel engines.
Electric equipment brings a huge plus - it's much quieter. The Volvo ECR25 electric excavator runs at 84 dB while its diesel counterpart hits 93 dB. This 9 dB drop makes it sound about twice as quiet. Workers can communicate better on noisy construction sites.
Battery life and charging considerations on active jobsites
Runtime matters a lot to contractors. Electric excavators run 4-6 hours on one charge during normal use. This works well for most standard workdays when machines start and stop. Equipment size and manufacturer determine the charging setup, with three main options:
- AC Level 1 charging (110V): Takes 24 hours for a full charge
- AC Level 2 charging (208-240V): Gets you running in about 6 hours
- DC Fast Charging: Quick 2-hour charge time
Sites without power access have smart options too. Manufacturers now offer solar chargers with sun-tracking panels that let you charge completely off-grid.
Performance in challenging environments and conditions
Electric construction equipment works well in temperatures from 14°F to 104°F (-10°C to 40°C). Lithium-ion tech handles cold better than older batteries. It loses less power and doesn't have memory effect issues.
The Electric Worksite project tested various electric machines between 3.5-30 tons in urban construction sites. Their research found that "in all tests, whatever the application and location, the electric machines performed as well as, if not better than, equivalent models with combustion engines, but without harmful emissions and disturbing noise".
Battery powered construction equipment now meets mainstream adoption needs. It delivers the technical performance you want plus environmental and operator benefits.
Implementation Strategies for Contractors of All Sizes
Your company's size doesn't matter when you plan to switch to electric equipment. Contractors need practical strategies because dozens of models are now available. These strategies will help make this change both manageable and profitable.
Starting small: Best entry-level electric equipment
Mini excavators and compact loaders are perfect first steps for contractors who want to try electric equipment. These smaller machines can run 3-6 hours on a single charge, which works well for most standard workdays with regular stop-start patterns. Companies like Volvo, Caterpillar, and JCB make electric mini excavators that perform just as well as diesel models but are 50% quieter. Case's 12EV wheel loader comes with a 23 kWh lithium-ion battery that matches its diesel counterpart's power and runs 3-6 hours per charge.
Creating charging infrastructure on construction sites
Your success depends on reliable charging solutions. You have three main options:
- AC Level 1 charging (110V): Complete charge within 24 hours
- AC Level 2 charging (208-240V): Full charge in approximately 6 hours
- DC Fast Charging: Reduces charging time to about 2 hours
Sites without grid access can use off-grid options such as solar chargers with sun-tracking panels. The Department of Energy reports that Level 2 charging infrastructure costs about USD 3500.00 per connector.
Training requirements for operators and maintenance staff
Equipment manufacturers provide three levels of certification in their training programs. Level 1 covers safety basics for operators with less than 3 years experience. Level 2 helps those with 3+ years experience work more efficiently. Level 3 leads to professional certification. These programs cost USD 750.00 per student per day at manufacturer facilities.
Phased replacement approaches for existing fleets
A step-by-step transition helps manage your costs:
- Start with equipment used indoors or in noise-sensitive areas
- Replace older equipment (15+ years) as maintenance costs rise
- Test electric machines through rentals before buying
- Add emission control devices to your current diesel equipment as a temporary solution
This gradual approach lets you build experience with electric equipment while keeping your operations running smoothly during the transition.
Case Studies: Success Stories from Early Adopters
Companies leading the way in construction prove that construction equipment electrification works in real life and brings clear benefits. Their stories teach valuable lessons to businesses looking to switch.
Urban construction projects using all-electric equipment
Skanska broke new ground with their pilot project on the Los Angeles Metro Purple Line extension. They showed what electric excavators could do in busy city environments. Their Volvo EC230 Electric excavator loaded haul trucks at a station dig site. The results were impressive - carbon emissions dropped by 66% and costs went down by 74% during the 90-day test. This 23-ton machine matched its diesel counterpart's output and ran much quieter in the enclosed space.
The Electric Worksite project in Gothenburg, Sweden tested several electric construction vehicles between 3.5-30 tons at actual building sites. Results showed that "electric machines performed as well as, if not better than, equivalent models with combustion engines, but without harmful emissions and disturbing noise". Public and private sectors worked together in this detailed study to prove electric equipment works well in cities.
Cost savings achieved by medium-sized contractors
Casper Company, a demolition and concrete cutting business near San Diego, put the Volvo ECR25 Electric excavator to work on indoor projects. They used this battery powered construction equipment to replace manual labor for underground utilities in occupied buildings. The benefits went beyond better operations. Casper noticed a big improvement in job site communication: "With this machine, operators and anyone around them can talk to each other". This led to safer and more productive work sites.
Turner Construction Company took a different path with their Meta data center project. Rather than buying equipment, Turner created a Contractor Controlled Equipment Program. This program helped trade partners get green construction equipment from Sunbelt Rentals on-site. Their mix of hybrid and electric machines cut emissions by 20-100%, depending on the type of equipment.
How small contractors are making the transition work
Walden Hill, a 400-acre farm in Massachusetts focused on sustainable forestry, became North America's first customer for Volvo's ECR25 Electric excavator. This small business choice matched their environmental goals: "Minimizing our carbon footprint is critical, so we try to do that with every decision we make". Before this, they switched between renting excavators and using their tractor for construction work.
Baltic Sands Inc., a small luxury developer in Southern California specializing in environmentally sensitive projects, added electric construction equipment to their fleet. Jacques Marais, their director, gives advice to other small contractors: "investigate what your operation is—really scrutinize what your existing units are doing on an average type of job". This helps find the best ways to bring in electric machines.
Conclusion
Electric construction equipment proves to be an excellent choice for contractors who want eco-friendly and cost-effective solutions. The original costs are higher than diesel options. However, this is a big deal as it means that reduced fuel usage, lower maintenance costs, and tax incentives make it a smart investment.
Tests in the field show that battery-powered machines work just as well as traditional equipment - sometimes even better. Companies like Volvo, Caterpillar, and JCB keep adding more electric options to their lineup. Rental companies now make these machines available to businesses regardless of their size.
Companies like Skanska and Turner Construction have shown that electric equipment's benefits go beyond helping the environment. Smaller contractors can begin with compact equipment such as mini excavators. This approach lets them build experience while they retain control of their operations.
Better batteries and increased production will make electric construction equipment more affordable. Companies that adopt this technology now keep up with trends. They'll be ready to meet the growing need for eco-friendly construction methods while gaining major operational benefits.