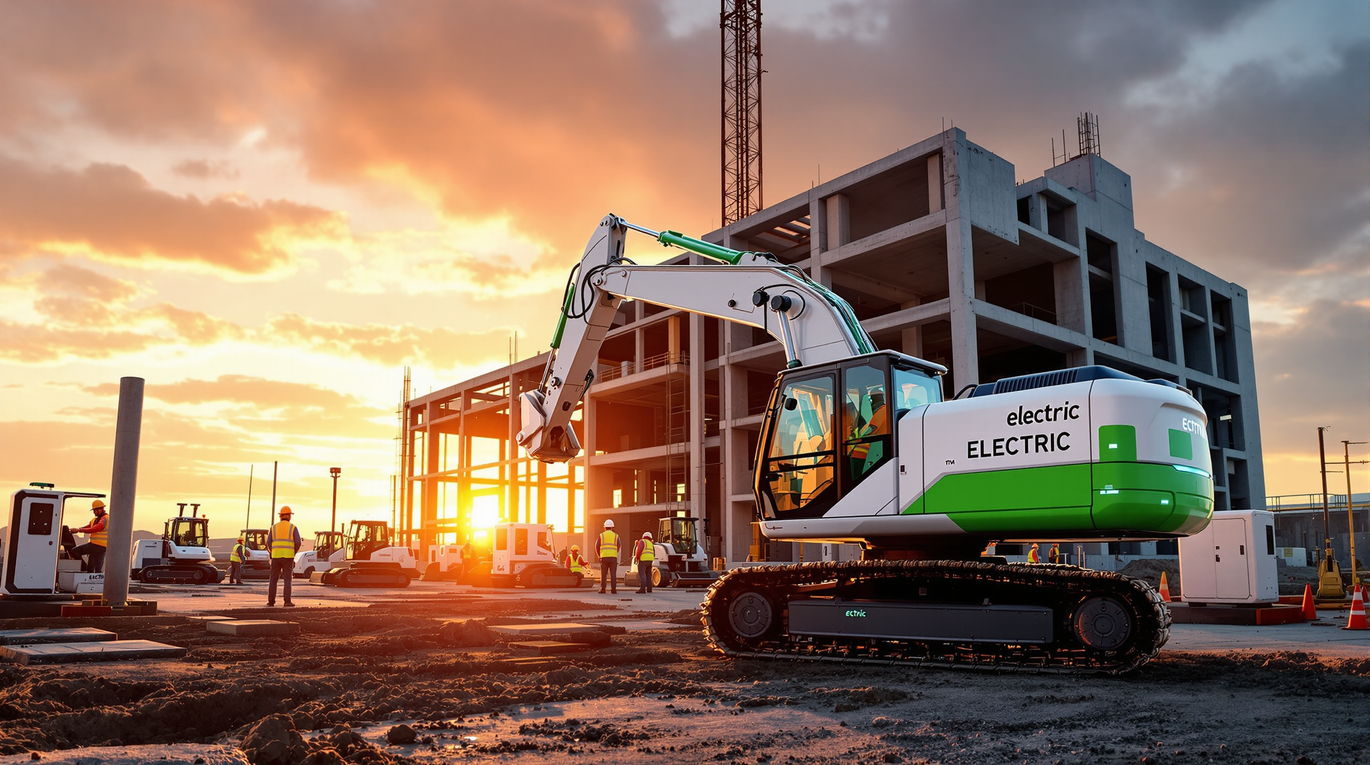
Construction equipment trends are shifting dramatically, with the electric machinery market projected to reach US$126 billion by 2044. While many assume electric equipment lacks power, today's electric mini-excavators actually deliver 30-60% more digging force than their diesel counterparts.
Despite these impressive capabilities, the electric construction equipment market still faces misconceptions. In fact, 78% of equipment dealers see electrification as a significant opportunity, yet many construction professionals remain skeptical. We've analyzed the latest data and spoken with industry experts to separate truth from fiction about construction equipment electrification. This reality check will help you understand what's actually happening in the industry and what to expect in 2025.
Current State of Electric Construction Equipment
The electric construction equipment sector is experiencing remarkable growth, with the global market value reaching USD 10.16 billion in 2023. Furthermore, industry projections indicate substantial expansion, anticipating the market to surge to USD 57.95 billion by 2032.
Market size and adoption rates
Currently, the adoption of electric construction machinery varies significantly across regions. Asia Pacific leads the market with a 34% share, primarily due to rapid urbanization and stringent emission regulations. Additionally, the market is witnessing a compound annual growth rate of 23.6%, indicating accelerating adoption rates across the construction industry.
Popular equipment types
Excavators dominate the current market landscape, accounting for 30% of all electric construction equipment sales. Notably, compact equipment has seen particularly strong uptake, especially in urban construction projects where noise and emission restrictions are stringent.
The equipment landscape includes:
- Electric mini excavators with 8-hour operational capacity
- Compact wheel loaders offering 3-6 hours of working autonomy
- Electric dump trucks with regenerative braking systems
- Battery-powered backhoe loaders and telehandlers
Leading manufacturers
Major industry players are actively expanding their electric equipment portfolios. Volvo Construction Equipment presently maintains the largest electric construction lineup, offering everything from compact excavators to midsize electric loaders. Moreover, manufacturers like Caterpillar and Komatsu have made significant strides, with Komatsu recently launching its first large electric excavators, the PC200LCE-11 and PC210LCE-11.
The market has subsequently witnessed several groundbreaking developments. For instance, Case Construction Equipment introduced its new compact electric wheel loader 12EV in 2024, featuring a 23kWh cobalt-free lithium-ion battery. Similarly, Mecalac unveiled the eMDX, the world's first 6-ton electric site dumper, capable of operating for eight hours on a single charge.
Battery technology plays a crucial role in current market dynamics. Lithium-ion batteries lead with 44% market share, offering superior energy density and longer lifespan compared to traditional alternatives. Nevertheless, manufacturers are exploring various power solutions, including hydrogen fuel cells, to address different operational requirements.
The construction sector currently represents 32% of the end-user market, followed closely by mining applications where electric equipment helps reduce ventilation costs and improve operational efficiency. Significantly, the industry is witnessing increased interest in rental and leasing services, making electric equipment more accessible to smaller contractors.
Common Misconceptions About Electric Equipment
Misconceptions about electric construction equipment often stem from outdated information and resistance to change. However, real-world data reveals a different story altogether.
Performance limitations
Contrary to popular belief, electric equipment delivers superior power efficiency. Electric motors convert approximately 85% of their electrical energy into motion, whereas internal combustion engines only manage about 40%. Electric machines provide instant torque at any RPM, enabling them to handle multiple functions simultaneously, unlike hydraulic systems that face limitations.
Cost savings reality
Although initial purchase prices run higher for electric equipment, operational savings offset this premium rapidly. The absence of fuel costs combined with reduced maintenance expenses results in considerable long-term savings. Electric machinery requires up to 50% fewer parts than diesel counterparts, consequently minimizing breakdown risks and service-related downtime
The cost advantage becomes even more apparent when considering:
- No expenses for filters, belts, or other moving parts
- Reduced cleanup costs
- Lower energy costs for charging versus diesel fuel
- Minimal service-related downtime
Battery life expectations
One persistent myth suggests that electric equipment requires frequent recharging and faces significant runtime limitations. However, field data demonstrates that most operators use their machines for 4-6 hours within a typical 8-hour workday. Interestingly, some early adopters found themselves charging their equipment every two to three days rather than daily.
The latest lithium-ion batteries offer several advantages over traditional power sources:
- No memory effect issues
- Maintenance-free operation
- Better performance in cold temperatures
- Rapid charging capabilities
To maximize battery longevity, operators should maintain charge levels between 20% and 90%. Through proper management, batteries can last approximately 10 years. Additionally, telematics systems actively monitor battery health, enabling proactive maintenance when necessary.
The reality of electric construction equipment surpasses common perceptions regarding performance, cost, and reliability. As technology continues advancing, these machines increasingly prove their worth across various construction applications, offering both environmental and operational benefits without compromising capability or efficiency.
Hidden Challenges Nobody Talks About
Beyond the widely discussed aspects of electric construction equipment, several critical challenges demand attention. These hurdles, often overlooked in initial discussions, can significantly impact implementation success.
Infrastructure requirements、
The shift toward electric construction equipment necessitates substantial changes in site infrastructure. According to industry data, a typical construction site requires 240-volt, Level 2 AC charging setups with SAE J1772 charging adapters for optimal charging times. Nonetheless, remote locations pose unique challenges, as they often lack access to reliable power grids.
For sites without direct grid access, contractors must consider alternative solutions. Solar charging stations offer one viable option, featuring panels that automatically adjust to track the sun's movement. Yet, these solutions require careful planning and additional investment.
The infrastructure demands extend beyond mere charging capabilities. Sites must accommodate:
- Upgraded electrical distribution systems
- Dedicated charging zones
- Enhanced safety protocols for high-voltage equipment
Training needs
The transition to electric equipment introduces complex training requirements. OSHA mandates comprehensive operator training, certification, and evaluation before personnel can operate new equipment. This training encompasses:
First, operators must master equipment-specific operational procedures. The training should cover proper charging protocols, battery management, and emergency response procedures. According to industry standards, operators need moderate-term on-the-job training, with median annual wages reaching USD 55,270.
Secondly, maintenance personnel require specialized training in electric systems. Since electric equipment features different component configurations, technicians must understand both mechanical and electrical aspects of these machines. The training must include safety protocols for working with high-voltage systems and battery maintenance procedures.
Interestingly, the Bureau of Labor Statistics projects a 4% growth in construction equipment operator jobs through 2033. This growth underscores the increasing importance of proper training programs. Furthermore, employers must provide retraining when operator performance indicates necessary improvement.
The complexity of these challenges often catches organizations off-guard, leading to implementation delays and unexpected costs. Therefore, thorough planning and understanding of these hidden challenges become crucial for successful electric equipment integration.
Real-World Implementation Success Stories
Success stories from real-world implementations demonstrate the practical benefits of electric construction equipment across diverse project scales. From small contractors to large-scale developments, these cases highlight the tangible advantages of electrification.
Small contractor experiences
Cox Construction, a family-owned business near Toronto, successfully integrated electric mini-excavators into their operations, proving these machines excel even in demanding tasks like breaking large rocks. The company reported substantial improvements in operational efficiency, with electric equipment matching or exceeding traditional diesel performance.
Art's Rental Equipment & Supply, another small-scale success story, expanded their business by offering electric construction equipment to clients. Their strategic decision paid off as customers increasingly sought sustainable solutions for urban construction projects.
Large project case studies
In Stockholm's Slakthusområdet district, a groundbreaking achievement showcases the potential of electric equipment adoption. The construction site achieved 50% electric equipment operation, utilizing two EC230 Electric crawler excavators and an L120H Electric Conversion wheel loader. This implementation resulted in dramatic reductions in CO2 emissions, dropping from the typical 11-29 tons to just 3.5 tons per SEK 1 million in turnover.
Skanska's Los Angeles D Line Subway Extension project presents another compelling case study. Their deployment of a Volvo CE 23-ton EC230 electric excavator led to remarkable results:
Meta's data center construction in Altoona, Iowa, spanning over 5 million square feet, incorporated various electric and hybrid equipment types. The project achieved emission reductions ranging from 20% to 100%, depending on the equipment used. Through innovative charging solutions and careful planning, the project maintained consistent operations while meeting sustainability goals.
These implementations consistently demonstrate that proper planning and infrastructure support enable successful electric equipment integration. The results consistently show improved operational efficiency, reduced emissions, and significant cost savings across different project scales.
Conclusion
Electric construction equipment has proven its worth beyond initial expectations. Market projections of USD 57.95 billion by 2032 reflect growing confidence in this technology. Real-world implementations, from small contractors like Cox Construction to large-scale projects like Stockholm's Slakthusområdet district, demonstrate that electric machinery delivers superior performance while reducing operational costs.
Though challenges exist with infrastructure requirements and training needs, companies actively addressing these hurdles report significant benefits. Data shows that electric motors offer 85% energy efficiency compared to 40% in combustion engines, while maintenance costs drop due to 50% fewer parts.
The construction industry stands at a turning point where electric equipment represents both environmental responsibility and business sense. Success stories across different project scales prove that proper planning and implementation lead to reduced emissions, lower operational costs, and improved site efficiency. These results suggest that electric construction equipment will become standard practice rather than an alternative option for forward-thinking contractors.